Like all my fellow Californians and many across the United States and the globe, I’ve been spending a lot more time at home, limiting my out-of-home trips to the essentials. And not surprisingly, all regional art shows have been postponed or cancelled, and commissioned work has also ground to a halt.
While I spent the first few weeks of our “shelter in place” building a few different designs of the incredibly labor-intensive end-grain coasters, in the hopes that art shows will start up again in 2021, I’ve dedicated a lot of my new-found free time to many small workshop improvements.
Almost all of these small projects (re)used materials sitting in my garage gathering dust, so is both recycling and taking advantage of a resource many of us have no shortage of these days: time.
Convenient Switches
With the tight space when the CNC is down from the lift, it was difficult to turn on the shop lights; I’ve put in a much-more convenient three-way switch.
The old setup led to ridiculous moments like this, where I’m reaching for the switch with a broom handle because the CNC and wood rack are keeping me from getting closer.
Behold! A switch. In the right place, it can change your world! (Yes, like many of us, I have recalibrated what I get excited about).
CNC Dust Collector Repair
The dust collection system for my CNC has been out of operation ever since I did the z-axis upgrades described here, due to both broken and no-longer-fitting parts.
First, I cut out the cross-brace that caused the problem, and fabricated the replacement orange plastic insert so the system would work mechanically.
I still use two of these, to control the DeWalt 611 Router cutting head and the vacuum pump clamp, but this can no longer control my 240v dust collection system.
I also connected it to my more powerful dust collection system rather than my small shop vac - the much larger filter surface area of my dust collector means that the vacuum system won’t get clogged when milling a jig from MDF as is needed on projects like this.
But connecting my larger 240v dust collector means I could no longer use this simple relay to automatically turn it on and off based on the CNC action. So I added a relay originally designed for air conditioner compressors so that the low voltage logic controller of my CNC could automatically trigger the 240v dust collector. And finally, I repositioned and added a pivot and spring-loaded cable to the X-Carve hose arm so that it will auto-retract as the CNC is lifted into the ceiling. Now setting up the CNC to use the vacuum takes mere seconds, so I have been using it much more frequently, keeping my shop cleaner.
I also connected it to my more powerful dust collection system rather than my small shop vac - the much larger filter surface area of my dust collector means that the vacuum system won’t get clogged when milling a jig from MDF as is needed on projects like this.
But connecting my larger 240v dust collector means I could no longer use this simple relay to automatically turn it on and off based on the CNC action. So I added a relay originally designed for air conditioner compressors so that the low voltage logic controller of my CNC could automatically trigger the 240v dust collector. And finally, I repositioned and added a pivot and spring-loaded cable to the X-Carve hose arm so that it will auto-retract as the CNC is lifted into the ceiling. Now setting up the CNC to use the vacuum takes mere seconds, so I have been using it much more frequently, keeping my shop cleaner.
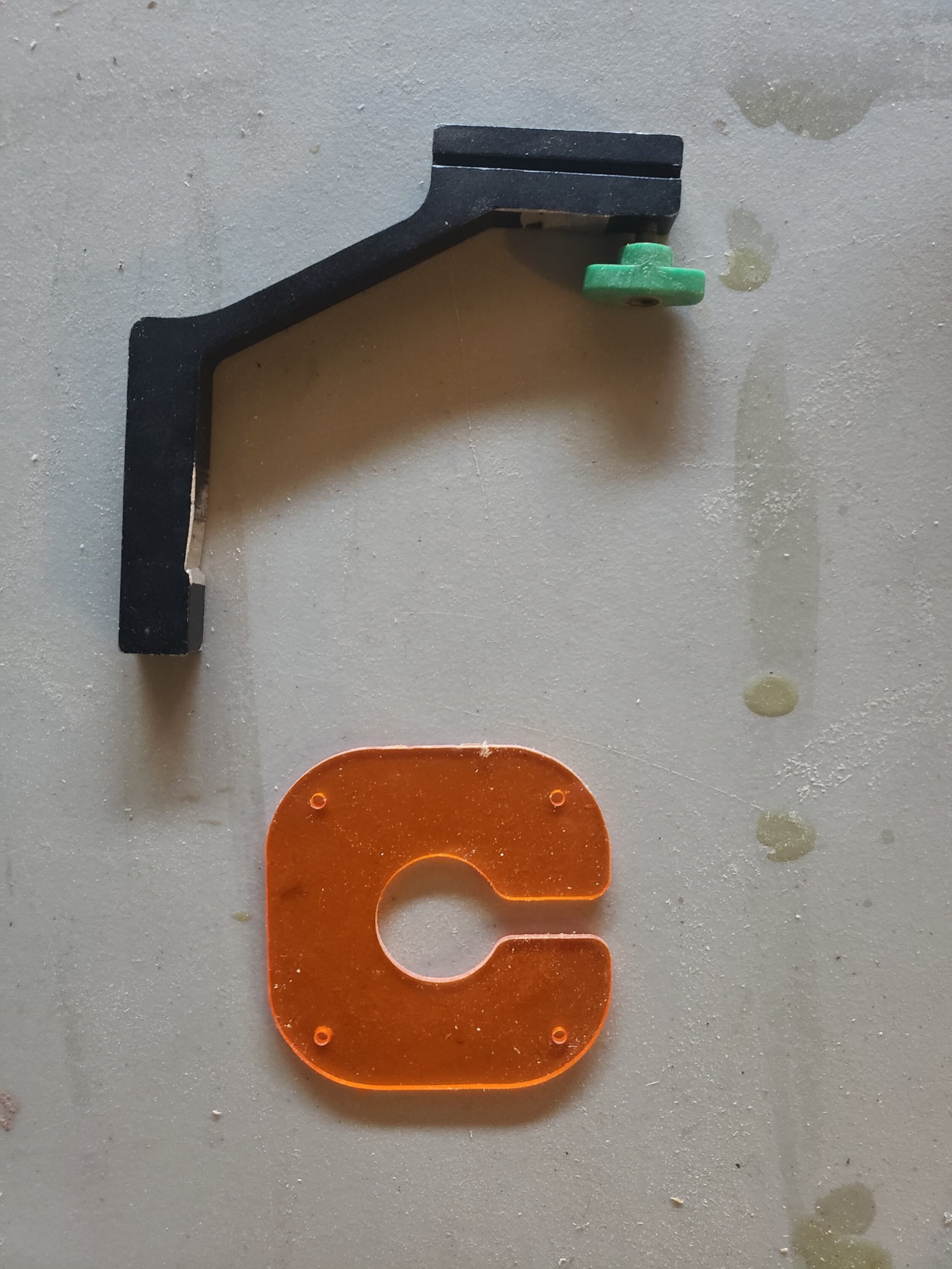
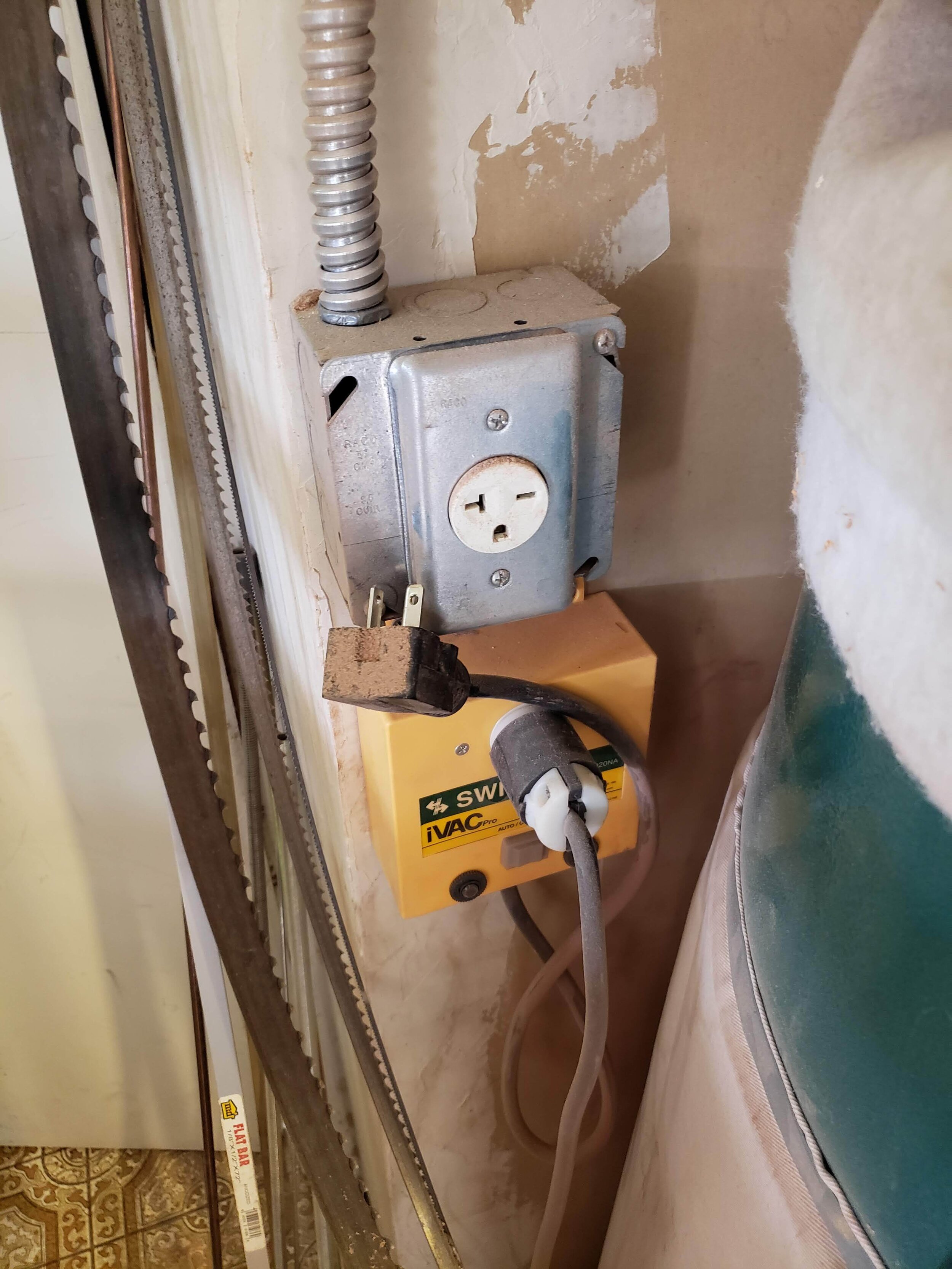
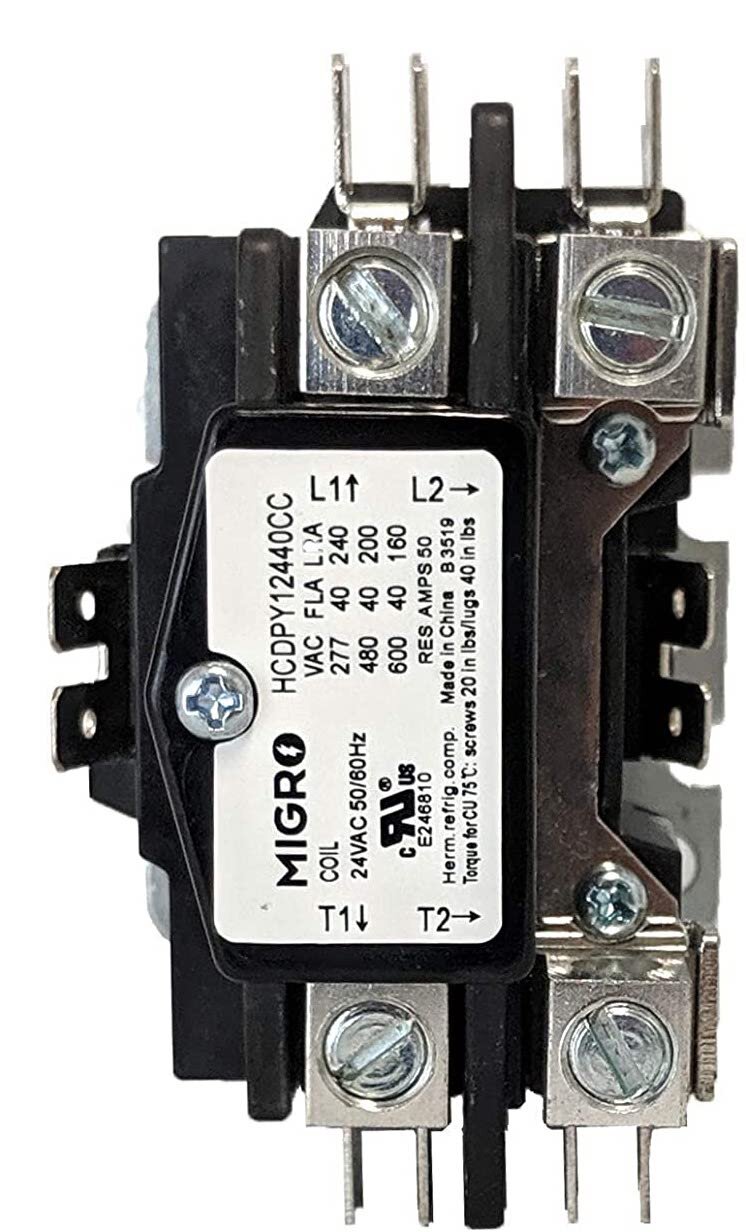
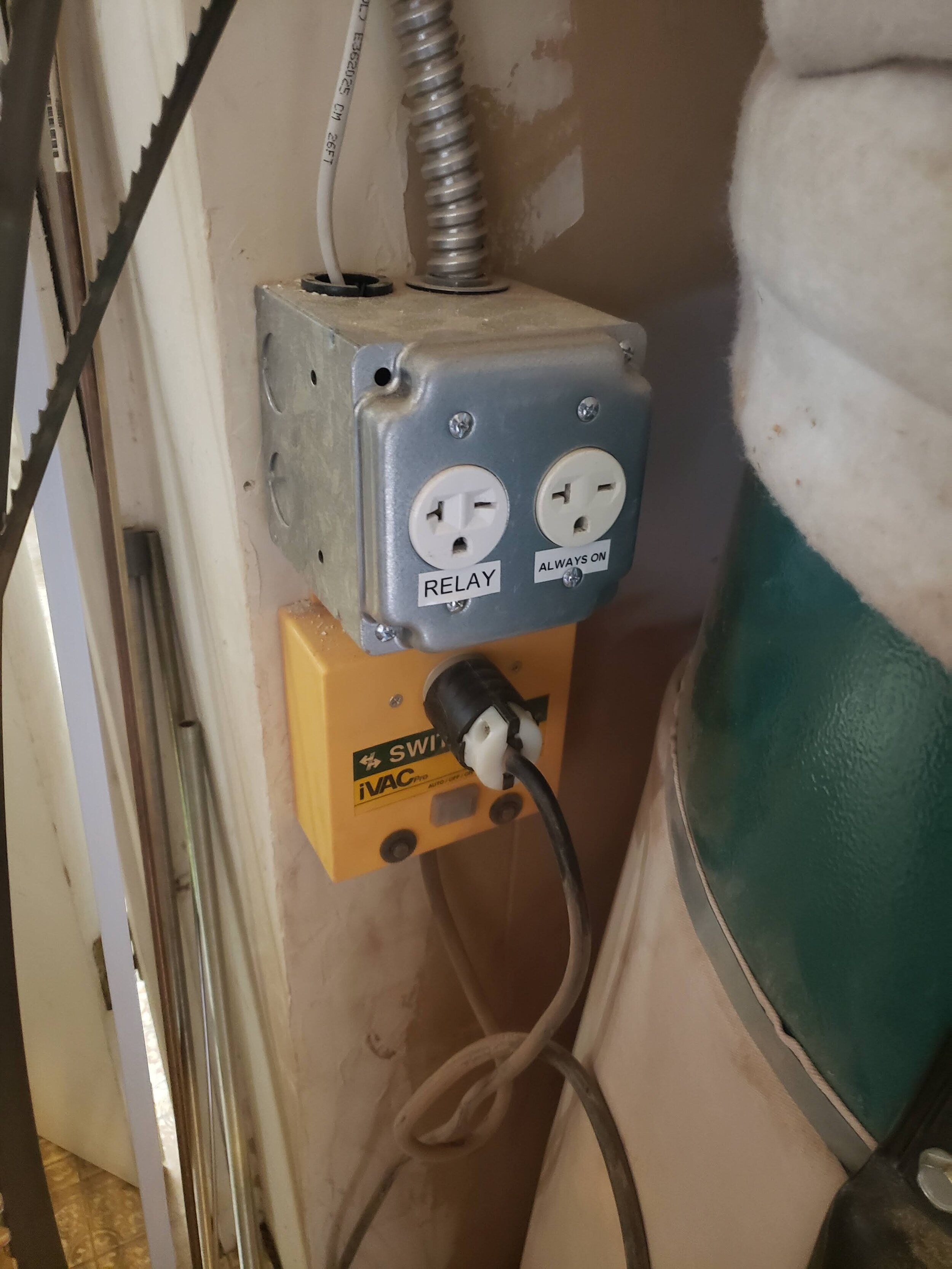

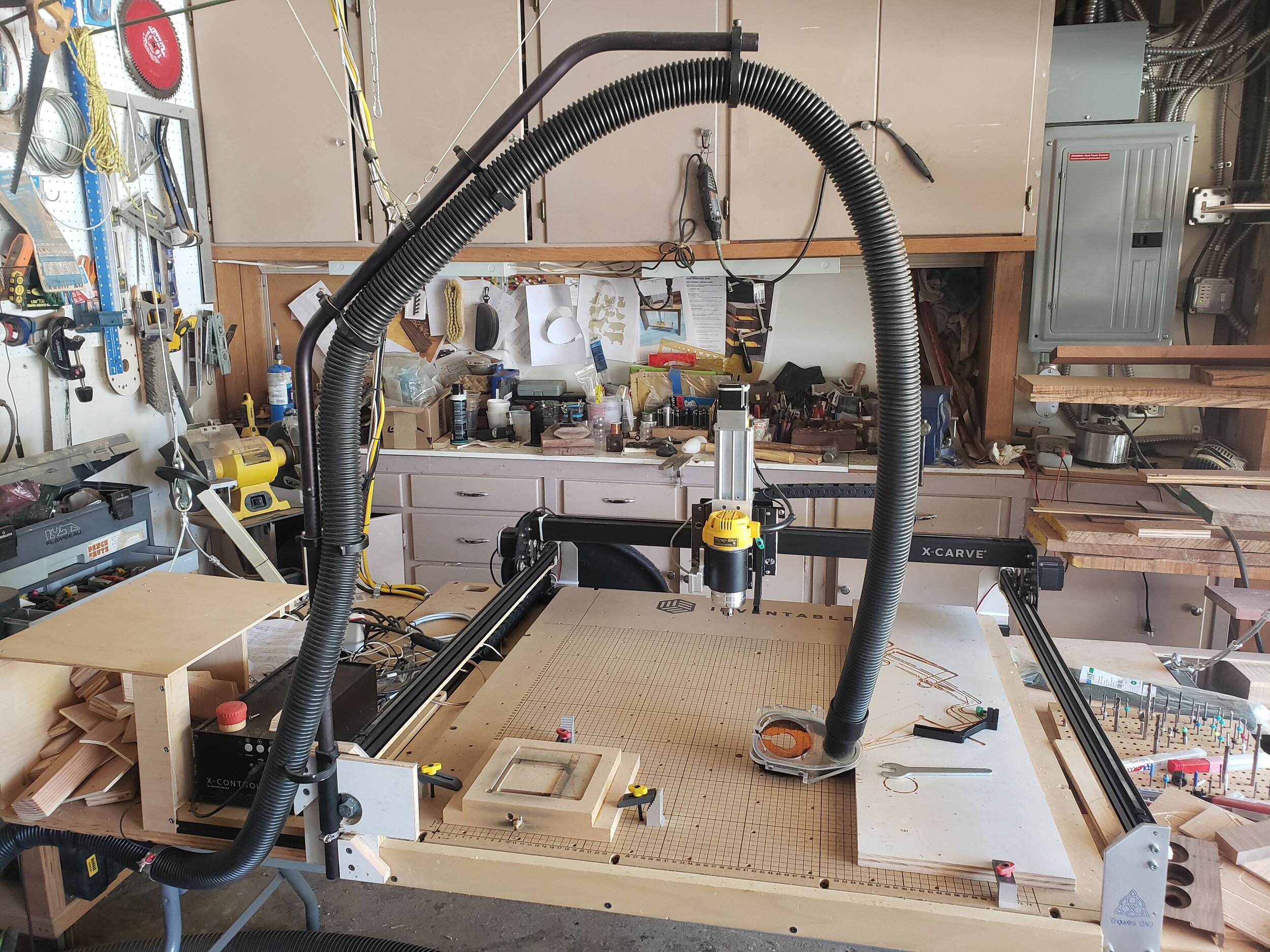
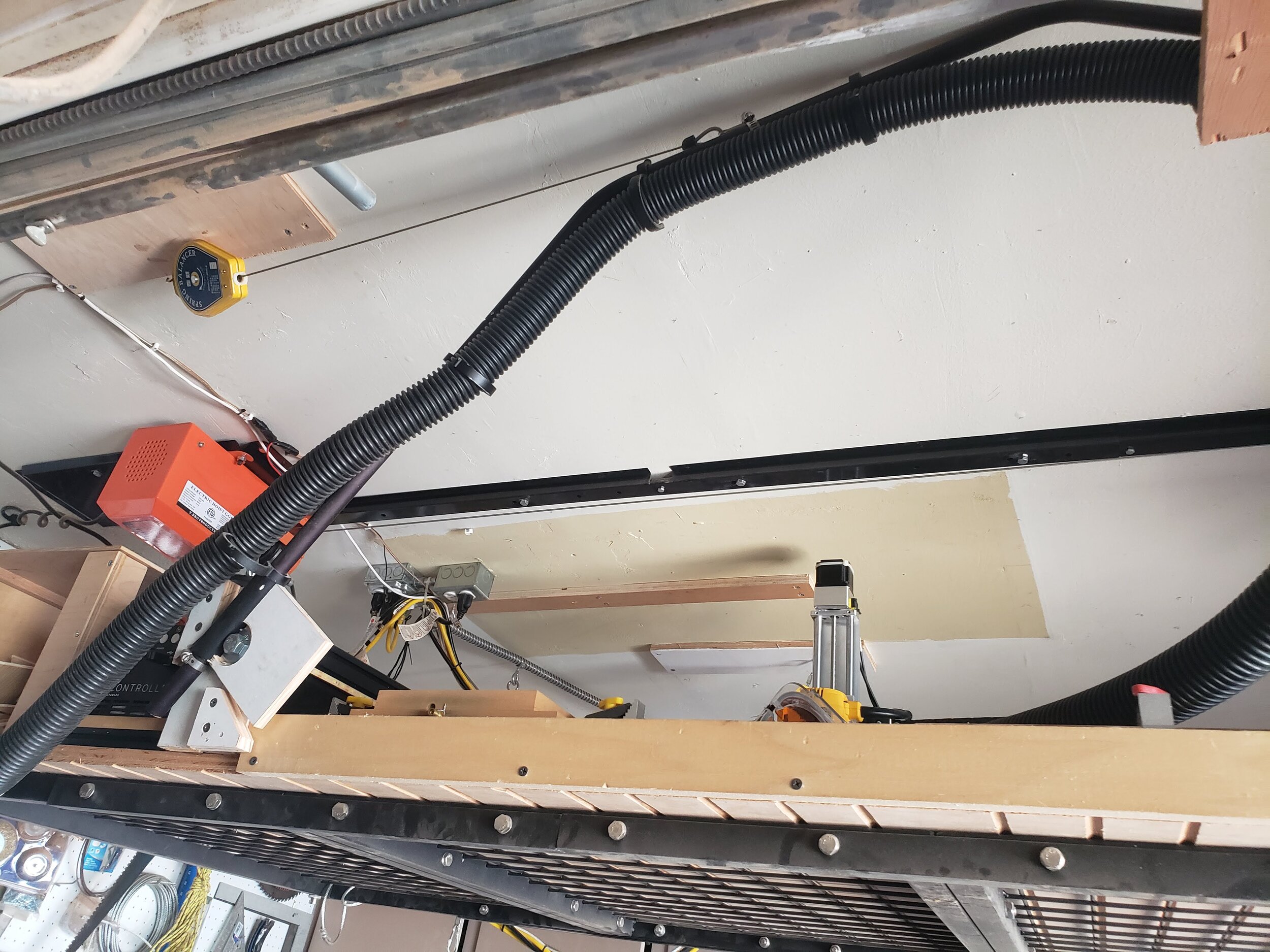
CNC Electrical Routing
My CNC uses three electrical circuits - one for cutting head and the electronics, one for the vacuum pump clamp to hold coasters in place for engraving, and now one for the 240v shop vacuum. This was both a mess of high and low voltage cords going back and forth, as well as confusing to continuously swap plugs to make sure that the CNC could control the separate circuits when it was in use, but yet that I could manually control the dust collector and vacuum pump when the CNC was not in use.
I addressed all these issues with the installation of a unique 3-way switch and some basic cable strapping combined with another one of those spring-loaded retractable cables.
This nifty three-position DPDT center-off switch, combined with a few relays, allows me to control all the systems in a much more integrated way.
Though I don’t have a before-picture, you can trust that this more compact cabling is a lot safer, and provides more space.
Shelving
Stud-bay narrow shelves.
Finally, no workshop improvement series would be complete without the addition of some new storage and shelves, though perhaps mine is a little unique as I make space of smaller and smaller spaces! The aisle between my lumber rack and wall provided some space for a few shelves, as long as I found a way to use the space in between the studs as well; my CNC also now has a perch for the laptop, so I no longer need to balance it precariously on the drill press work table.
Lots of Coasters
I’ve also been making lots and lots of coasters - they’ve been very popular in past art shows, and, like the workshop improvements, they make use of materials I already have but - especially for these end grain coasters - take a huge amount of labor to build. I’ve restocked all my foreign language coasters, and added Portuguese to the set as well.
Wrapping Up
Have you also had lots open time to fill, as your social plans get upended and summer travels get curtailed? Or have your days gotten more packed with new childcare and education responsibilities? I’d love to hear - and regardless, stay safe, sane, and healthy in these challenging times.